Procesos más eficientes, precisos, optimizados y sostenibles: así son las últimas tecnologías que se utilizan en la producción de autos.
Ejemplo de ello es el Audi e-tron GT, el primer modelo de la marca que se planeó completamente sin prototipos físicos.
Pero ¿entonces cómo lo hicieron? Con escaneos de edificios en tres dimensiones, los procesos de aprendizaje automático y el uso de la realidad virtual.
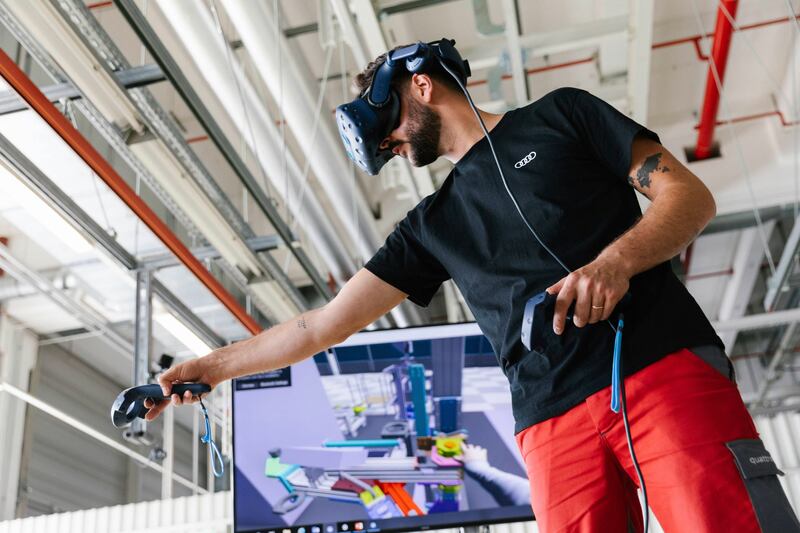
Incluso, todos los procesos de ensamblaje, como los procedimientos y las acciones de los empleados, se probaron y optimizaron en espacios virtuales.
Y no sólo eso: la compañía comparte que la planificación virtual se extiende al trabajo a distancia, digital y conectado, sin viajes o asignaciones al extranjero.
Así era antes
El objetivo de los prototipos es definir y optimizar los procesos de producción posteriores. Generalmente, se utilizan diferentes prototipos que se fabrican durante la fase de planificación inicial.
Estos modelos están hechos con piezas construidas a mano. ¿La desventaja? El tiempo y el costo. Por ejemplo, Audi señala que en esta fase, deben de responderse las siguientes preguntas:
¿Cuáles son las tareas del empleado? ¿Dónde debe ubicarse una pieza para que el empleado tenga un acceso óptimo a ella? ¿Puede el empleado sostener e instalar la pieza por sí mismo? ¿Cómo tiene que moverse para hacerlo? ¿Hay otras partes en el camino? ¿Qué herramientas necesita?
Pero ahora, y en el futuro, ya no será necesario usar un prototipo físico, por lo menos así fue con el Audi e-tron GT.
Así es el futuro
Con información de la marca, lo que se requiere de esta fase de planificación, ahora virtual, es garantizar que durante la producción posterior del vehículo, todos los procesos estén perfectamente engranados y los ciclos a lo largo de la línea estén perfectamente coordinados.
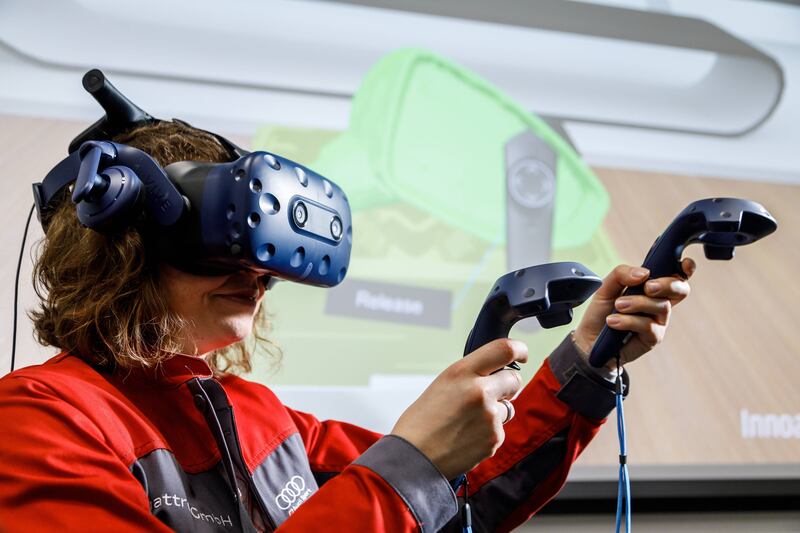
Como te imaginarás esto requiere tal nivel de precisión, que sólo es posible haciéndolo a escala. Y es aquí donde entran los escaneos 3D.
Estos crean una reproducción virtual de la instalación de producción física, incluidos todos los equipos, herramientas y estantes.
Para ello, el escáner, el hardware, es esencial para generar los datos correspondientes:
– Tiene aproximadamente dos metros de altura y está montado sobre cuatro ruedas para que un empleado pueda moverlo por los espacios.
– En la parte superior hay una unidad LiDAR (detección de luz y rango) y tres escáneres láser adicionales, así como una cámara. Se llevan a cabo dos procesos simultáneamente mientras se escanea un espacio: la cámara gran angular toma una fotografía del espacio, mientras que los láseres la miden con precisión y generan una nube de puntos tridimensional del entorno 250 mil metros cuadrados de espacio de la nave de producción en la planta de Neckarsulm.
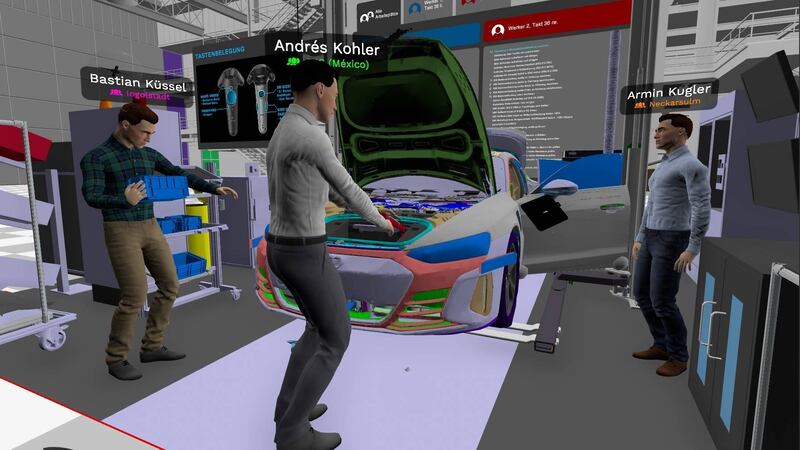
– Finalmente, es la interacción entre el hardware y el software lo que toma los puntos, las imágenes y los conjuntos de datos generados y los convierte en una imagen general utilizable que se puede utilizar con los sistemas de planificación existentes.
– El software utilizado está basado en inteligencia artificial y aprendizaje automático. La nube de puntos y las fotografías se combinan para producir un espacio fotorrealista tridimensional similar al que se ve en Google Street View. También aprende automáticamente con cada escaneo para reconocer, distinguir y clasificar objetos con mayor precisión. Por ejemplo, el sistema distingue entre un estante y una viga de acero.
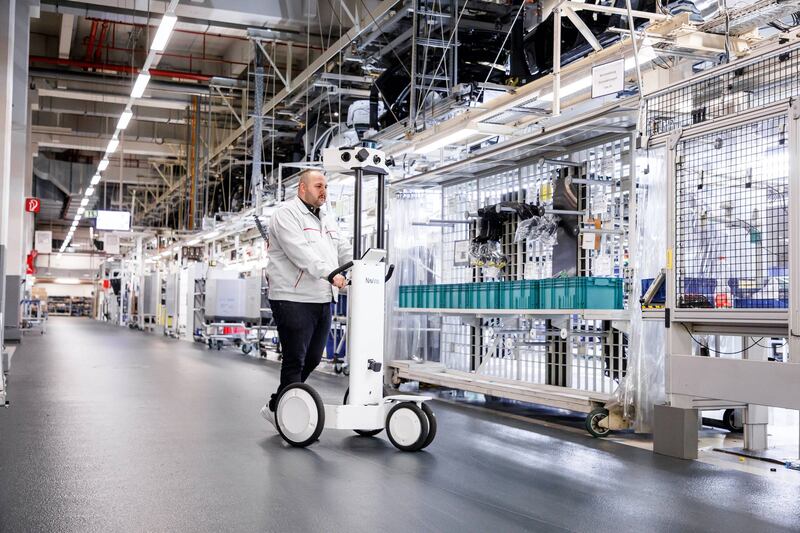
¿La mayor ventaja? Que no importa dónde se encuentren las personas a nivel mundial, ahora pueden reunirse en espacios virtuales y encontrarse en medio de las instalaciones de producción.
Otra es la sostenibilidad. El hacer así las planificación ocasiona menos recursos, desperdicio ¡y viajes de negocios!
¡También en México!
Un taller 3P, es decir, de proceso de preparación de la producción, se llevó a cabo en la planta de Audi en San José Chiapa, México, donde participaron miembros del equipo del proyecto de Ingolstadt.
Así lo hicieron como avatares digitales de forma totalmente virtual. Allí fue posible que los expertos planificaran la producción del facelift del Audi Q5 y el nuevo Q5 Sportback en realidad virtual.
¿Qué te parece?
#elfuturodelautoeshoy